The manufacturing industry is the fifth largest employer in the U.S. It’s also experienced a period of rapid growth over the last few decades.
It’s an exciting industry to be a part of. But, like every other sector, manufacturing faces its fair share of challenges. Organizations must overcome these hurdles to continue being successful in 2020 and beyond.
Here are four common problems the manufacturing industry faces today:
1. The manufacturing skills gap
One of the biggest manufacturing challenges U.S. businesses face is the growing skills gap.
The country has an aging workforce consisting mainly of baby boomers. As such, the manufacturing sector desperately needs skilled, younger workers. (Approximately 22% of existing skilled manufacturing workers will be retiring by the end of 2025.)
Unfortunately, there aren’t currently enough workers to fill these roles. According to the Manufacturing Institute, there could be as many as two million unfilled manufacturing jobs by 2025.
Yet the growth in manufacturing over the last few decades means companies need skilled workers now more than ever. So how can the manufacturing industry tackle this growing skills gap?
Join 10,000 companies solving the most complex people problems with PI.
Hire the right people, inspire their best work, design dream teams, and sustain engagement for the long haul.
Here are four possible solutions:
Partnering with educational institutions.
This can ensure more young people are aware of the benefits of a career in manufacturing. In fact, more and more manufacturing companies have been doing this. Case in point: 32% of Generation Z has had a manufacturing career suggested to them, compared to only 18% of Millennials.
Embracing a more flexible way of working.
More and more people want to work into their retirement years. Manufacturers can ease the process by offering flexible work hours. A flexible working package like this can also include opportunities to work remotely.
Upskilling existing lower-skilled employees.
Companies can encourage a culture of learning with in-house mentoring and training programs. This could help you optimize your talent by moving people into new roles within the company as they gain the necessary skills.
To ensure a new role is a good behavioral fit for an employee, use The Predictive Index to create a behavioral Job Target for the role then compare it to the employee’s Reference Profile. Why does behavioral job fit matter? When a person’s a fit for their job, they’re more likely to be engaged and go the extra mile!
Implementing programs like internships and on-the-job training.
Doing so can entice millennials and Gen Xers in other industries to make the leap to manufacturing. There’s no one-size-fits-all solution to bridging the manufacturing skills gap. Rather, smart manufacturers will implement a multi-pronged approach to the issue.
2. Inventory and supply chain management
Managing your supply chain and inventory is crucial to any manufacturing business. As companies look to ramp up production, they also need better, more agile manufacturing processes. As such, manufacturers have begun embracing the need for digital transformation.
Inventory management is a common problem in the manufacturing industry. Holding too little inventory can hurt both profits and the relationship with customers. Keeping too much inventory can be costly to store and difficult to sell. So investing in the right software and processes to track and manage inventory can save manufacturers time and money.
Real-time tracking enables manufacturers to monitor and manage the flow of raw materials. It also lets them track work in process and finished products. This level of insight means companies can prevent inventory issues by intervening at first sign of a problem.
The impact of supply chain problems has become topical in the wake of the Coronavirus (COVID-19) outbreak. Many manufacturers source parts from China—most notably computer and electronic components. And these companies are already feeling the sting of the supply chain disruption.
Digital transformation can support more agile importing and supply chain management. And through dual-sourcing, companies can reduce their reliance on one supplier for raw materials. These steps can reduce manufacturers’ exposure to the risk of supply chain interruptions.
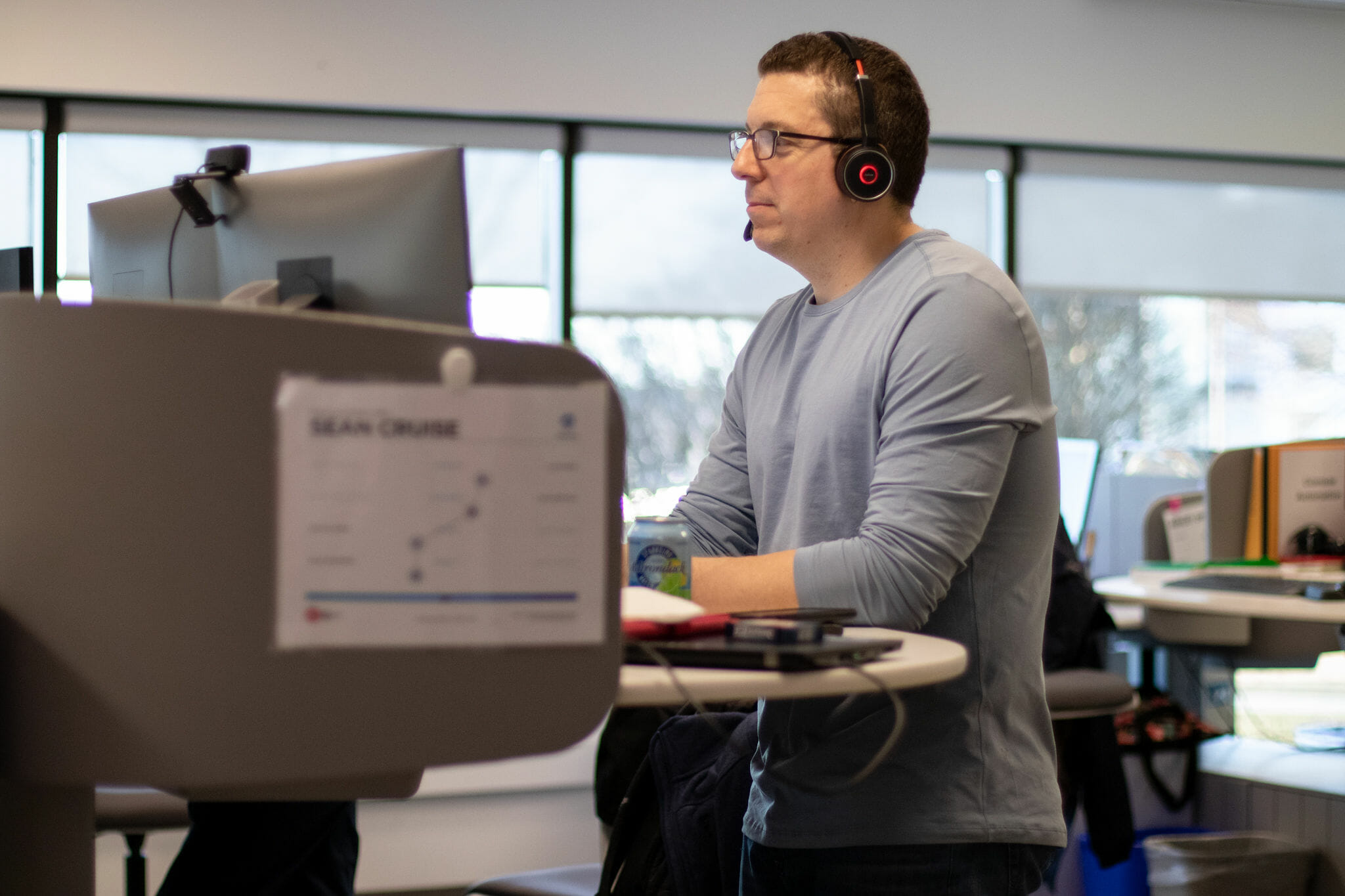
3. The Internet of Things (IoT)
The internet of things is opening up a world of opportunity for consumers and manufacturers alike. The popularity of fitness trackers and smart home devices shows no signs of slowing down. More and more customers expect to be able to connect their devices to products like fire alarms, doorbells, and refrigerators.
When it comes to health and medical devices, the IoT provides exciting opportunities for patients and healthcare providers. Continuous glucose monitors are one example. These items use the industrial Internet of Things to let people monitor and manage their diabetes through a smartphone app.
Beyond consumer devices, the Internet of Things has also created opportunities for manufacturers. Connected machines on the shop floor let manufacturers collect real-time data. They even let companies complete remote machine diagnostics and repairs.
Manufacturers that want to stay ahead need to identify how they can use the IoT to its full potential. Used correctly, it can enable manufacturers to maximize efficiency and meet operational targets. The capability to collect a lot of data is enticing. But without a strategy to analyze and act upon them, those data become less valuable.
4. Incorporating robotics and automation
Automating production lines can help manufacturing companies produce more in less time. But implementing automation and bearing the upfront cost of robotics poses specific challenges. The good news is those challenges are more than outweighed by the benefits.
Efficiency on the shop floor is crucial for manufacturers. By implementing robotics and automation, companies can increase production rates. They can also reduce safety risks, improve product quality, and increase customer satisfaction.
Customers expect high-quality, reliable products at increasingly reduced costs. The best way to achieve this is with automation.
Automation also has a valid place in the strategy to reduce the manufacturing skills gap. Companies can upskill lower-skilled workers whose roles would normally be replaced by automation. This lets you perform more complex tasks while easing employee fears about new technologies.
Ushering in the new age of manufacturing
Ultimately, these common problems the manufacturing industry faces are opportunities to strengthen the sector. This is incredibly exciting, as it can provide new and enriching employment opportunities.
Manufacturing has a long and rich history as a vital part of the U.S economy. The manufacturing sector is also used to adapting to changes and overcoming challenges. Over the next decade, it’s the organizations willing to meet these challenges head-on that will not only survive, but thrive.